制造業(yè)ERP軟件系統(tǒng)定制開發(fā)
大家好,我們是成都小火軟件,今天是2025年5月16日,星期五。上一篇文章,我介紹了政務(wù)類軟件的定制開發(fā)。目前市面上有政企類成品軟件,但是只能“照顧”到部分的政企,因?yàn)橹荒茏龆ㄖ崎_發(fā),包括訓(xùn)練自己的大模型,定制開發(fā)AI功能等。ERP軟件幾乎是企業(yè)的“標(biāo)配”,企業(yè)根據(jù)自身的業(yè)務(wù)需求、組織架構(gòu)、運(yùn)營流程等,進(jìn)行定制化的ERP軟件開發(fā)。
今天我們深入探討汽車制造、電子設(shè)備、醫(yī)療器械等不同細(xì)分領(lǐng)域的ERP定制需求,重點(diǎn)剖析各行業(yè)所需的特色功能開發(fā)方案,揭示專業(yè)定制開發(fā)如何助力制造企業(yè)突破管理瓶頸。
一、汽車零部件制造:定制化生產(chǎn)排程與供應(yīng)鏈協(xié)同
行業(yè)痛點(diǎn)
某汽車轉(zhuǎn)向系統(tǒng)制造商面臨多品種、小批量混線生產(chǎn)難題,原有ERP系統(tǒng)無法處理400余種標(biāo)準(zhǔn)件的動(dòng)態(tài)排產(chǎn)需求,物料配送精準(zhǔn)度不足導(dǎo)致生產(chǎn)線停工待料率達(dá)15%。
定制解決方案
1. 智能排產(chǎn)引擎:開發(fā)基于遺傳算法的多目標(biāo)排產(chǎn)模塊,同時(shí)優(yōu)化設(shè)備利用率、換線成本和交貨期。系統(tǒng)自動(dòng)生成包含300+工序的詳細(xì)生產(chǎn)計(jì)劃,并實(shí)時(shí)展示各產(chǎn)線負(fù)載狀態(tài)。
2. 供應(yīng)商協(xié)同平臺(tái):對(duì)接30+核心供應(yīng)商系統(tǒng),通過EDI接口實(shí)現(xiàn)電子物料清單(JIT)自動(dòng)補(bǔ)貨,緊急訂單處理時(shí)間從4小時(shí)縮短至30分鐘。
3. 質(zhì)量追溯系統(tǒng):為每件產(chǎn)品生成唯一識(shí)別碼,記錄從原材料檢驗(yàn)到裝配測(cè)試的全流程數(shù)據(jù),實(shí)現(xiàn)批次質(zhì)量問題的30秒快速定位。
實(shí)施效果:生產(chǎn)線換模時(shí)間降低40%,物料配送準(zhǔn)確率提升至98%,年節(jié)約庫存成本超800萬元。
二、電子設(shè)備制造:多維度成本分析與柔性生產(chǎn)
行業(yè)痛點(diǎn)
一家消費(fèi)電子代工廠商需要處理300+SKU的快速迭代,現(xiàn)有ERP無法準(zhǔn)確核算工單級(jí)成本,頻繁的設(shè)計(jì)變更導(dǎo)致訂單履約率僅有75%。
定制解決方案
1. 動(dòng)態(tài)BOM管理:建立可配置物料清單系統(tǒng),支持客戶定制參數(shù)(如顏色、存儲(chǔ)容量)的快速調(diào)整,新產(chǎn)品導(dǎo)入周期由7天壓縮到3天。
2. 生產(chǎn)成本核算矩陣:開發(fā)包含原材料成本、設(shè)備折舊、人工工時(shí)、能源消耗的四維成本分析模型,精確計(jì)算每單位產(chǎn)品的實(shí)際成本。
3. 產(chǎn)能彈性預(yù)警:搭建生產(chǎn)負(fù)荷預(yù)測(cè)系統(tǒng),通過機(jī)器學(xué)習(xí)算法分析歷史訂單數(shù)據(jù),提前14天發(fā)出產(chǎn)能瓶頸預(yù)警。
技術(shù)實(shí)現(xiàn):采用微服務(wù)架構(gòu)分割訂單管理、MRP、成本核算模塊,通過容器化部署實(shí)現(xiàn)快速迭代。關(guān)鍵業(yè)務(wù)接口采用GraphQL提升數(shù)據(jù)查詢效率。
轉(zhuǎn)型成果:產(chǎn)品交付準(zhǔn)時(shí)率提升至92%,通過精準(zhǔn)成本控制增加高附加值訂單占比,毛利率提升6個(gè)百分點(diǎn)。
三、醫(yī)療器械制造:法規(guī)遵循與全生命周期追溯
行業(yè)痛點(diǎn)
III類醫(yī)療器械制造商面臨GMP合規(guī)壓力,現(xiàn)有ERP系統(tǒng)缺乏審計(jì)追蹤功能,產(chǎn)品在6個(gè)環(huán)節(jié)的質(zhì)量數(shù)據(jù)無法有效串聯(lián),影響CE/FDA認(rèn)證審核。
定制解決方案
1. 法規(guī)遵從框架:內(nèi)置ISO 13485、21 CFR Part 11標(biāo)準(zhǔn)模塊,自動(dòng)記錄所有操作日志并生成符合審計(jì)要求的報(bào)告。
2. UDI編碼集成:與全球醫(yī)療器械數(shù)據(jù)庫(GUDID)對(duì)接,實(shí)現(xiàn)產(chǎn)品唯一設(shè)備標(biāo)識(shí)(UDI)的自動(dòng)化生成與管理。
3. 臨床數(shù)據(jù)接口:搭建臨床試驗(yàn)結(jié)果導(dǎo)入接口,將產(chǎn)品測(cè)試數(shù)據(jù)與生產(chǎn)批次關(guān)聯(lián),形成完整的產(chǎn)品追溯鏈條。
4. 變更控制管理:開發(fā)設(shè)計(jì)變更(DCR)流程管控模塊,確保每次圖紙修改、工藝調(diào)整都經(jīng)過完整的風(fēng)險(xiǎn)評(píng)估與審批。
數(shù)據(jù)安全:部署符合HIPAA標(biāo)準(zhǔn)的加密存儲(chǔ)系統(tǒng),所有患者信息均進(jìn)行脫敏處理,關(guān)鍵數(shù)據(jù)實(shí)時(shí)同步到異地容災(zāi)中心。
應(yīng)用價(jià)值:通過FDA檢查一次通過率100%,產(chǎn)品召回周期從14天縮短到48小時(shí),客戶投訴減少58%。
四、家具制造業(yè):設(shè)計(jì)協(xié)同與柔性供應(yīng)
行業(yè)痛點(diǎn)
定制家具企業(yè)需要處理大量客戶化設(shè)計(jì)需求,常規(guī)ERP無法整合CAD圖紙與生產(chǎn)計(jì)劃,生產(chǎn)損耗率高達(dá)18%。
定制解決方案
1. CAD-ERP集成接口:開發(fā)IFC文件解析引擎,將設(shè)計(jì)師的3D模型自動(dòng)分解為工藝路線,材料利用率提升至85%。
2. 材料優(yōu)選系統(tǒng):根據(jù)產(chǎn)品結(jié)構(gòu)特性推薦替代材料,通過成本-性能模型為每個(gè)訂單設(shè)計(jì)最優(yōu)原材料組合。
3. 模塊化報(bào)價(jià)引擎:建立參數(shù)化報(bào)價(jià)模型,客戶修改尺寸或材質(zhì)后30秒內(nèi)生成新報(bào)價(jià),銷售轉(zhuǎn)化率提高35%。
4. 全屋配送規(guī)劃:整合物流系統(tǒng)數(shù)據(jù),優(yōu)化多訂單合單配送路徑,降低物流成本25%。
創(chuàng)新功能:通過AR增強(qiáng)現(xiàn)實(shí)技術(shù)實(shí)現(xiàn)虛擬裝配,在線展示客廳家具組合效果,提升客戶體驗(yàn)與轉(zhuǎn)化率。
業(yè)務(wù)影響:訂單轉(zhuǎn)化率提升28%,生產(chǎn)周期縮短至7天,市場(chǎng)占有率增長(zhǎng)12個(gè)百分點(diǎn)。
五、包裝印刷行業(yè):色彩管理與印版管理
行業(yè)痛點(diǎn)
高端包裝印刷商難以保證批次間顏色的一致性,傳統(tǒng)庫存管理導(dǎo)致印版報(bào)廢率達(dá)12%。
定制解決方案
1. 色彩控制模塊:集成分光光度計(jì)數(shù)據(jù),建立色彩偏差補(bǔ)償模型,實(shí)現(xiàn)印刷色彩實(shí)時(shí)監(jiān)控與自動(dòng)調(diào)整。
2. 印版生命周期管理:追蹤每塊印版從設(shè)計(jì)到報(bào)廢的全歷程,提供磨損預(yù)警并優(yōu)化調(diào)度,印版平均使用壽命延長(zhǎng)30%。
3. 菲林文件管理:開發(fā)專用的版式文件存儲(chǔ)格式,支持多版本并存與快速調(diào)用,版面錯(cuò)誤減少至0.5%以下。
4. 印刷產(chǎn)能優(yōu)化:根據(jù)紙張幅面、印刷機(jī)色組配置智能排產(chǎn),提升設(shè)備OEE(綜合效率)至88%。
系統(tǒng)集成:與ERP系統(tǒng)對(duì)接,實(shí)現(xiàn)從訂單接收到樣張確認(rèn)的閉環(huán)管理,縮短新產(chǎn)品打樣周期至72小時(shí)。
經(jīng)濟(jì)效益:訂單處理速度提升40%,廢品率降低18%,年節(jié)約生產(chǎn)成本約500萬元。
六、化工制造:批次追溯與環(huán)境合規(guī)
行業(yè)痛點(diǎn)
精細(xì)化工企業(yè)難以追蹤每批次產(chǎn)品的生產(chǎn)參數(shù),環(huán)保數(shù)據(jù)采集不及時(shí)導(dǎo)致多次超標(biāo)排放。
定制解決方案
1. 反應(yīng)過程管控:對(duì)接DCS系統(tǒng),實(shí)時(shí)采集攪拌速度、溫度、壓力等數(shù)據(jù),建立工藝參數(shù)數(shù)據(jù)庫。
2. 多批次追溯鏈:從原油采購到最終產(chǎn)品實(shí)現(xiàn)全過程跟蹤,精準(zhǔn)定位污染源,事故處理時(shí)間縮短80%。
3. 環(huán)境監(jiān)測(cè)集成:自動(dòng)采集排放數(shù)據(jù)并與環(huán)保局平臺(tái)對(duì)接,超標(biāo)預(yù)警響應(yīng)時(shí)間縮短至5分鐘。
4. 安全庫存模型:基于化學(xué)反應(yīng)動(dòng)力學(xué)建立原料消耗預(yù)測(cè)模型,優(yōu)化庫存水平,減少高危品庫存量。
特殊功能:開發(fā)在線預(yù)警系統(tǒng),當(dāng)工藝參數(shù)偏離設(shè)定范圍時(shí),自動(dòng)觸發(fā)工藝參數(shù)恢復(fù)流程及警報(bào)通知。
轉(zhuǎn)型成果:產(chǎn)品合格率提升至99.5%,環(huán)保處罰次數(shù)降為零,年度節(jié)約危化品存儲(chǔ)成本300萬元。
七、食品飲料制造:配方管理與批次追溯
行業(yè)痛點(diǎn)
休閑食品企業(yè)面臨多條生產(chǎn)線共用配方資源問題,傳統(tǒng)系統(tǒng)無法跟蹤單個(gè)批次的原料供應(yīng)商信息。
定制解決方案
1. 配方保密機(jī)制:采用權(quán)限分級(jí)與加密存儲(chǔ)雙重保障,確保核心配方安全,開發(fā)"影子配方"功能保護(hù)商業(yè)機(jī)密。
2. 配料批次追溯:記錄每批產(chǎn)品所使用的具體原料批次,支持供應(yīng)商來料檢驗(yàn)數(shù)據(jù)追溯,質(zhì)量追溯時(shí)間從2小時(shí)縮短到2分鐘。
3. 保質(zhì)期智能預(yù)警:基于生產(chǎn)批次和存儲(chǔ)條件動(dòng)態(tài)計(jì)算剩余保質(zhì)期,自動(dòng)觸發(fā)先進(jìn)先出(FIFO)提示。
4. 快速新品開發(fā)模塊:提供標(biāo)準(zhǔn)化配料庫,支持新產(chǎn)品快速配置與模擬生產(chǎn),樣品制作周期縮短60%。
功能亮點(diǎn):通過AR增強(qiáng)技術(shù)展示食品制作過程,支持消費(fèi)者掃描包裝碼查看原料產(chǎn)地與加工信息,提升品牌透明度。
經(jīng)濟(jì)效益:產(chǎn)品投訴下降45%,研發(fā)周期縮短50%,年節(jié)約質(zhì)量成本800萬元。
八、裝備制造:項(xiàng)目管理與售后服務(wù)
行業(yè)痛點(diǎn)
重型機(jī)械制造商需要跟蹤價(jià)值百萬設(shè)備的安裝調(diào)試進(jìn)度,現(xiàn)有ERP缺乏項(xiàng)目型管理功能,服務(wù)響應(yīng)滯后影響客戶滿意度。
定制解決方案
1. 項(xiàng)目管理系統(tǒng):集成甘特圖與資源平衡模型,實(shí)時(shí)跟蹤設(shè)備組裝、測(cè)試、發(fā)運(yùn)等各階段進(jìn)度。
2. 服務(wù)工單管理:連接物聯(lián)網(wǎng)(IoT)設(shè)備,當(dāng)客戶設(shè)備出現(xiàn)異常時(shí)自動(dòng)觸發(fā)服務(wù)工單,服務(wù)響應(yīng)時(shí)間縮短50%。
3. 備件智能預(yù)測(cè):基于設(shè)備運(yùn)行數(shù)據(jù)和歷史故障模式,預(yù)測(cè)備件需求,缺貨率減少70%。
4. 售后知識(shí)庫:收集整理常見故障解決方案,通過移動(dòng)端應(yīng)用現(xiàn)場(chǎng)指導(dǎo)維修,首次修復(fù)率從65%提升至89%。
系統(tǒng)特色:開發(fā)AR遠(yuǎn)程協(xié)助功能,專家可通過客戶攝像頭實(shí)時(shí)指導(dǎo)維修,減少差旅成本40%。
實(shí)施成效:項(xiàng)目交付準(zhǔn)時(shí)率從68%提升至92%,客戶滿意度調(diào)查得分提高27分,服務(wù)收入增長(zhǎng)40%。
制造業(yè)ERP系統(tǒng)的定制開發(fā)已經(jīng)成為企業(yè)數(shù)字化轉(zhuǎn)型的關(guān)鍵路徑。相較于標(biāo)準(zhǔn)化方案,定制開發(fā)能夠針對(duì)性地解決各細(xì)分領(lǐng)域的實(shí)際問題,如汽車行業(yè)的混線生產(chǎn)、醫(yī)療設(shè)備的法規(guī)合規(guī)、包裝行業(yè)的色彩控制等。通過定制,企業(yè)可以整合先進(jìn)的生產(chǎn)技術(shù)、管理方法和數(shù)字化工具,實(shí)現(xiàn)生產(chǎn)過程的智能化、管理決策的數(shù)據(jù)化、業(yè)務(wù)運(yùn)營的協(xié)同化。在小火軟件看來,制造業(yè)ERP系統(tǒng)將向著更加智能、協(xié)同、綠色的方向發(fā)展,為企業(yè)創(chuàng)造更大的價(jià)值和競(jìng)爭(zhēng)優(yōu)勢(shì)。
文章來源網(wǎng)址:http://www.shmme.net/archives/xitongkaifa01/1850,轉(zhuǎn)載請(qǐng)注明出處!
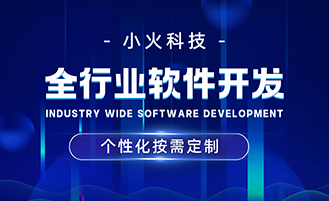

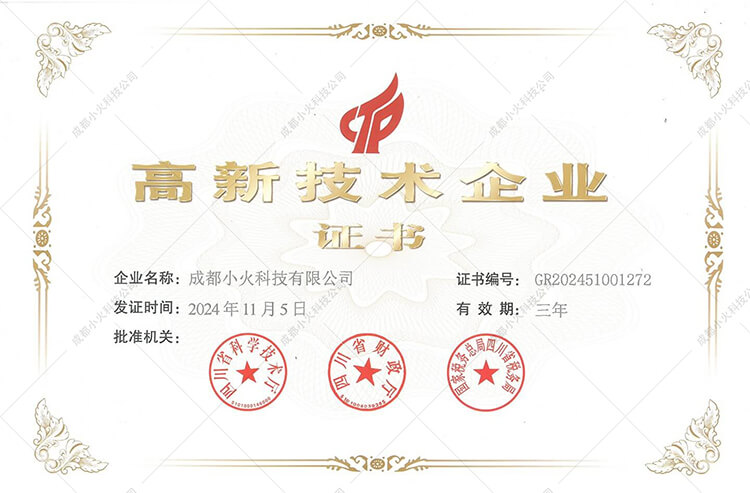
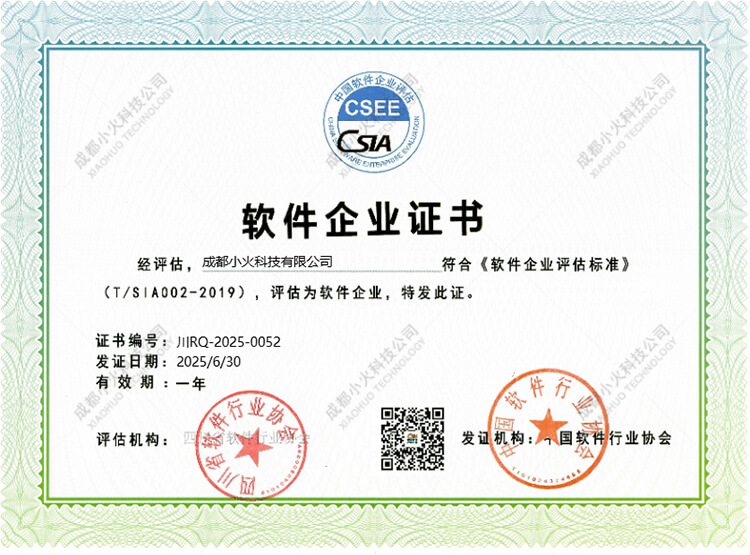
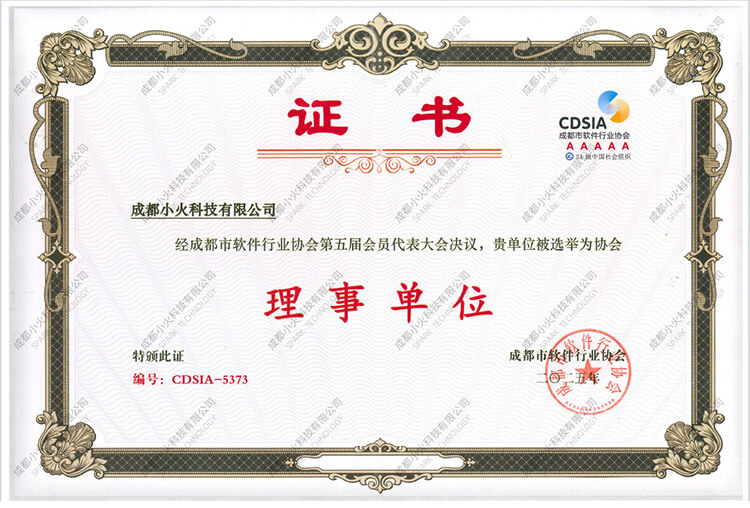
精選案例
推薦文章
Core competence
高質(zhì)量軟件開發(fā)公司-成都小火科技
多一套方案,多一份選擇
聯(lián)系小火科技項(xiàng)目經(jīng)理,免費(fèi)獲取專屬《項(xiàng)目方案》及開發(fā)報(bào)價(jià)
咨詢相關(guān)問題或預(yù)約面談,可以通過以下方式與我們聯(lián)系
業(yè)務(wù)熱線 19113551853

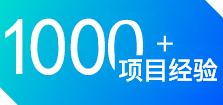